Comprehending Porosity in Welding: Exploring Reasons, Results, and Avoidance Strategies
As professionals in the welding market are well mindful, understanding the causes, impacts, and prevention techniques related to porosity is essential for achieving durable and reputable welds. By diving into the root causes of porosity, analyzing its destructive results on weld quality, and exploring efficient prevention methods, welders can enhance their knowledge and skills to create premium welds constantly.
Usual Reasons For Porosity
Contamination, in the type of dust, grease, or rust on the welding surface area, creates gas pockets when heated up, leading to porosity in the weld. Improper protecting takes place when the shielding gas, frequently used in processes like MIG and TIG welding, is incapable to fully safeguard the liquified weld pool from reacting with the surrounding air, resulting in gas entrapment and succeeding porosity. Additionally, insufficient gas insurance coverage, frequently due to inaccurate circulation rates or nozzle positioning, can leave parts of the weld unguarded, permitting porosity to form.
Impacts on Weld High Quality
The existence of porosity in a weld can dramatically endanger the overall quality and integrity of the welded joint. Porosity within a weld develops gaps or dental caries that deteriorate the framework, making it much more vulnerable to breaking, corrosion, and mechanical failing.
In addition, porosity can prevent the efficiency of non-destructive testing (NDT) methods, making it testing to spot various other problems or gaps within the weld. This can result in significant safety and security problems, especially in crucial applications where the architectural honesty of the bonded elements is critical.

Avoidance Techniques Review
Offered the damaging effect of porosity on weld quality, effective avoidance techniques are essential to keeping the architectural stability of welded joints. Among the key prevention techniques is extensive cleansing of the base materials before welding. Pollutants such as oil, oil, rust, and wetness can contribute to porosity, so making sure a tidy work surface area is necessary. Appropriate storage space of welding consumables in completely dry conditions is additionally vital to prevent moisture absorption, which can result in gas entrapment during welding. Additionally, choosing the appropriate welding specifications, such as voltage, existing, and travel rate, can help lessen the threat of porosity formation. Making certain sufficient securing gas flow and protection is an additional crucial avoidance technique, as inadequate gas insurance coverage can result in atmospheric contamination and porosity. Ultimately, proper welder training and accreditation are essential for executing preventative measures successfully and continually. By including these avoidance techniques into welding practices, the incident of porosity can be substantially lowered, leading to stronger and much more trustworthy bonded joints.
Significance of Correct Protecting
Proper securing in welding plays an essential function in stopping atmospheric contamination and making sure the stability of welded joints. Shielding gases, such as argon, helium, or a combination of both, are generally utilized to safeguard the weld swimming pool from reacting with elements airborne like oxygen and nitrogen. When these reactive elements enter call with the hot weld swimming click to find out more pool, they can trigger porosity, resulting in weak welds with reduced mechanical homes.
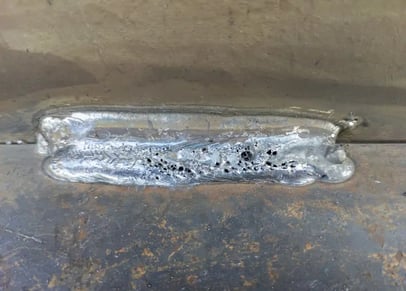
Insufficient shielding can lead to various flaws like porosity, spatter, and oxidation, compromising the architectural honesty of the welded joint. Consequently, adhering to correct shielding methods is essential to create top quality welds with marginal defects and make sure the long life and reliability of the bonded parts (What is Porosity).
Tracking and Control Methods
Exactly how can welders properly monitor and regulate the welding procedure to make certain optimal results and avoid problems like porosity? One key method is with the usage of innovative monitoring modern technologies. These can include real-time monitoring systems that offer comments on specifications such as voltage, present, take a trip rate, and gas circulation rates. By constantly checking these variables, welders can determine deviations from the perfect conditions and make immediate adjustments to avoid porosity development.

Furthermore, executing proper training programs for welders is vital for monitoring and managing the welding procedure efficiently. What is Porosity. Enlightening welders on the importance of preserving consistent parameters, such as appropriate gas securing and travel speed, can aid prevent porosity problems. Normal assessments and certifications can additionally guarantee that welders are skilled in surveillance and managing welding procedures
Moreover, using automated welding systems can boost monitoring and control capacities. These systems can specifically regulate welding specifications, minimizing the chance of human mistake and guaranteeing regular weld high quality. By incorporating advanced surveillance technologies, training programs, and automated systems, welders can properly keep track of and regulate the welding process to lessen porosity defects and accomplish top quality More Help welds.